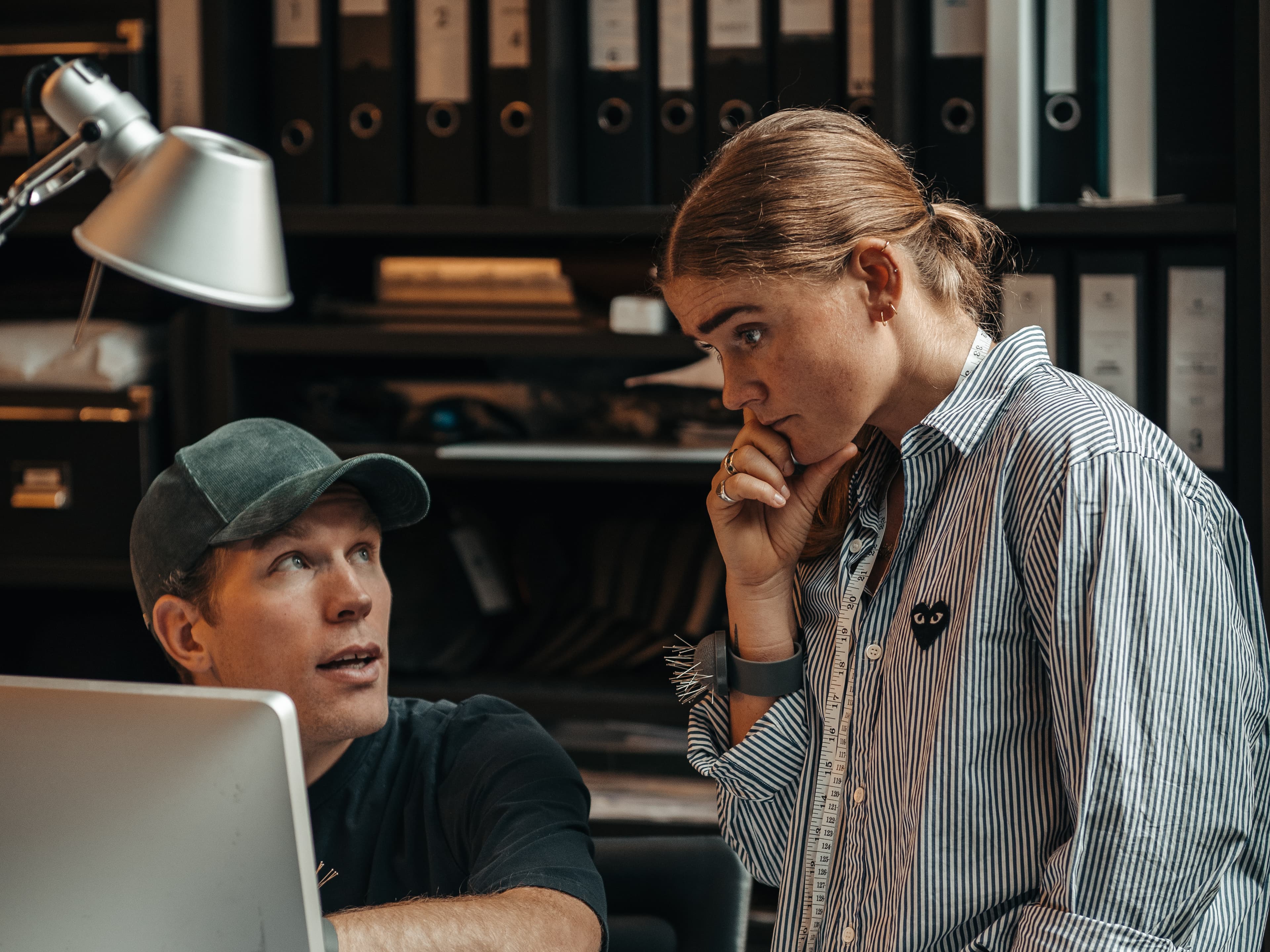
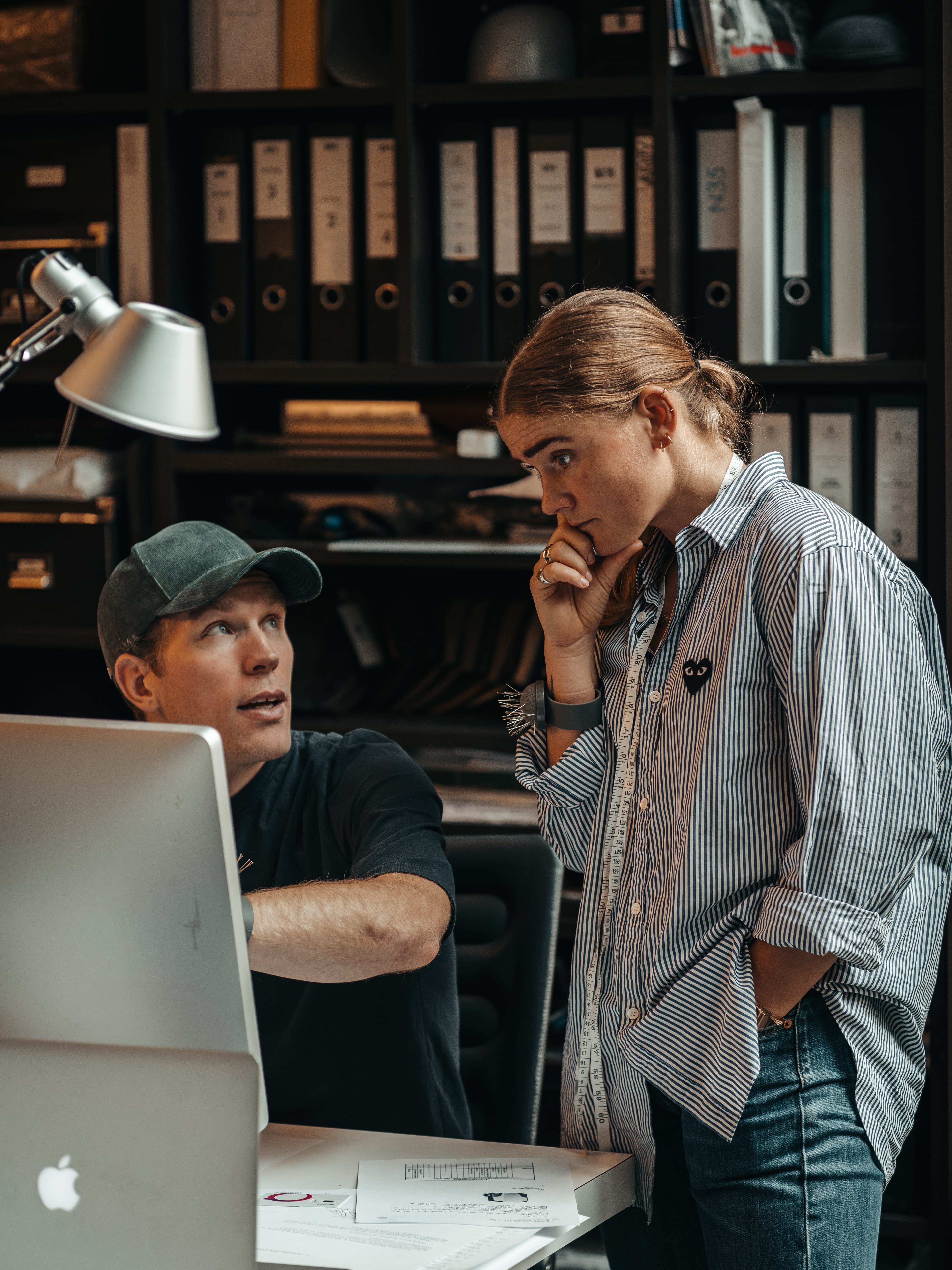
Behind the Design: Our Process
The Pursuit of Perfection
“We started Varsity Headwear with one mission – to design the perfect cap. This pursuit of perfection has influenced everything we have done from day one.
Although perfection is extremely hard to achieve, constantly refining and improving has led us to be product specialists we are today. We learn new things, discover new technology and are always trying to better understand the ever-changing trends and wishes of our customers. Our definition of perfection is constantly changing, but regardless, we find it very inspirational and motivating to try to always strive to improve our products and processes.”
– Alex & Seb
Inspiration and Development
We divide our collections into two categories: seasonal and non-seasonal. Our design team curates each seasonal collection to select patterns and fabrics that perform best in the specific seasonal weather. Our non-seasonal caps are available all year round, which typically include bestsellers and our sports range. We aim to always have stock in our non-seasonal caps.
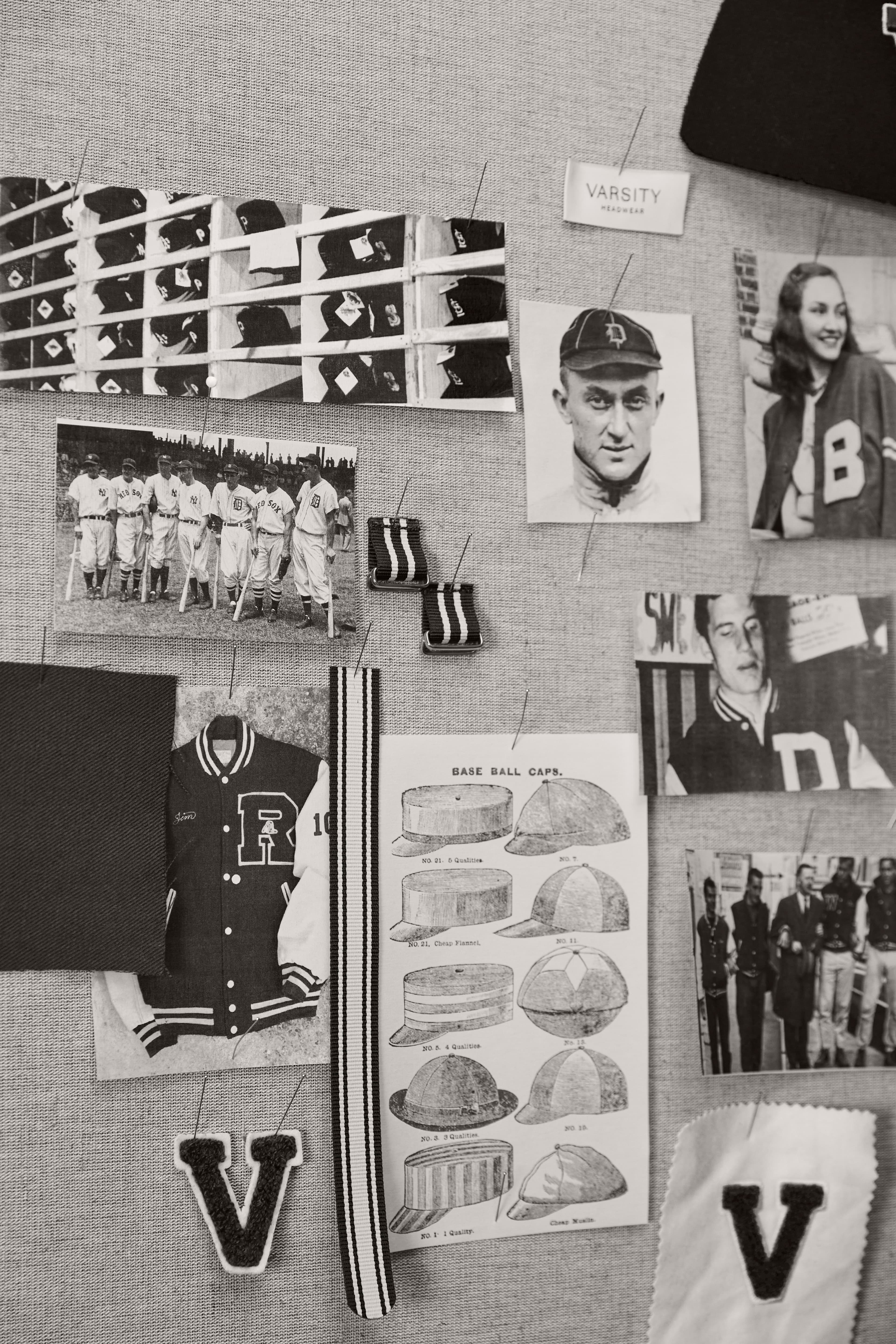
For the collection development, the design process starts with research and inspiration. Our design team studies upcoming trends, colors, patterns, and new technologies.
They also complete a review of past collections and customer feedback to better understand areas that we can improve. They make a general outline of the materials and caps they want to create for the next season. This collection can go through many rounds of changes and talks with the whole Varsity team to improve it.
Next, our design team sources the materials and textiles that suit the function of the cap best. The team moves the collection into the production planning phase and begins ordering. The typical design process can take upwards of 8-12 months from the initial idea to the final cap.
Sourcing from the world's best weavers and textile producers
The quality of our caps is a sum of three parts: textiles, craftsmanship, and customer care. The first two of which we can control, and the third of which we try to influence.
When we source materials for our caps, we aim high to use the best possible material to fulfill the cap’s purpose. For example, with a summer cap, we want it to be lightweight, durable, breathable, and elegant. Linen is a material that meets those requirements and makes up a large part of our “summer” collections.
Due to their small nature, our caps consume less material than most typical garments. We can therefore use higher-quality and more exquisite materials than many others in the fashion industry. We try to always use the “cleanest” possible compositions and natural materials to give the cap the best quality.
By "cleanest" we mean avoiding combining many different fibers into a textile. We use 100% Italian linen instead of a mix of linen and another material like cotton.
In some cases, we mix fibers to achieve a certain price point and functionality. Take, for example, our Athletic Sport Series. We use man-made fibers because they provide us with the best possible combination of quality, function, and aesthetics.
Most of the highest quality textile mills operate in Europe, where we weave the majority of the materials we use today.
We get our Linen and Cashmere from Italy. Our Cotton and Athletic Sport fabric comes from Switzerland. We source our Oilskin caps from their original producer in Scotland, and our SEAQUAL® YARN is from Portugal.
In addition to the main exterior fabric of a cap, there are several other important textiles and components we use.
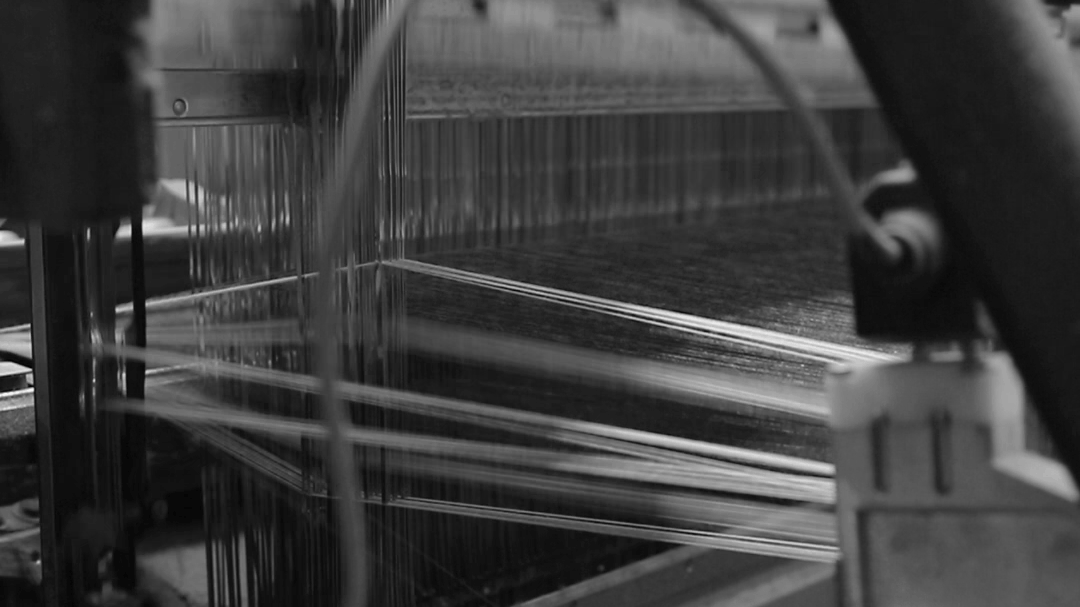
Assembly
In our typical cap, we have around 7-9 different suppliers from around the world. We believe our caps are only as good as their parts. Therefore, we work hard to find the best components. We choose each part for its quality, look, and usefulness.
Once we have the design, materials, and components ready, we then assemble them into the highest quality cap possible. Our two external partner factories in Vietnam and Estonia handle the manufacturing process.
We began producing our signature Varsity Headwear caps in Vietnam in 2013. In the past ten years, we have improved our products and processes. Our skilled team in Vietnam helps us create what we believe is the highest quality available.
Our team visits both factories regularly, and we work actively to promote a good working environment at the factory. Our team completes all assembly at one of our two factories before we ship the cap to our warehouse in Norway. We are always searching for new manufacturing partners worldwide. However, few meet our strict standards for work environment and quality.
Prototyping & Quality Control
We aim to test new developments as soon as possible by prototyping and sampling. To truly understand the changes and improvements we are making, we need to see, touch, and feel the caps in person.
Before a cap reaches your head, it has typically gone through multiple rounds of prototyping and testing. We found and sourced many fabric options for the Intensity Sport Series. We tested the initial material with members of our Owner’s Club. Finally, we chose the one that we think works best for our customers.
The final price
We hope that once you understand the entire process, our prices will seem justified and reasonable. The prices you see today come from careful preparation, sourcing, and manufacturing.
Good treatment of all workers is also important for a Varsity Headwear cap. For us, it's important to give our customers “value for money.” You can view the entire breakdown of our caps below.
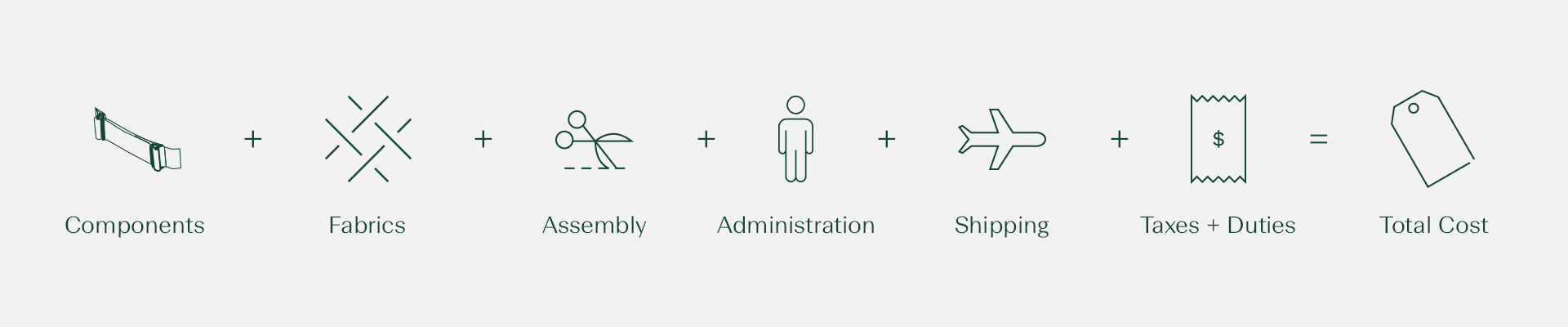
As cap specialists, we rely on our customers coming back. Our main goal is to provide the best service and product to every customer. We want to learn and grow continuously.
If you have any feedback on the design process we shared, please reach out to hello@varsityheadwear.com. Thank you for being a part of the journey!
Related articles
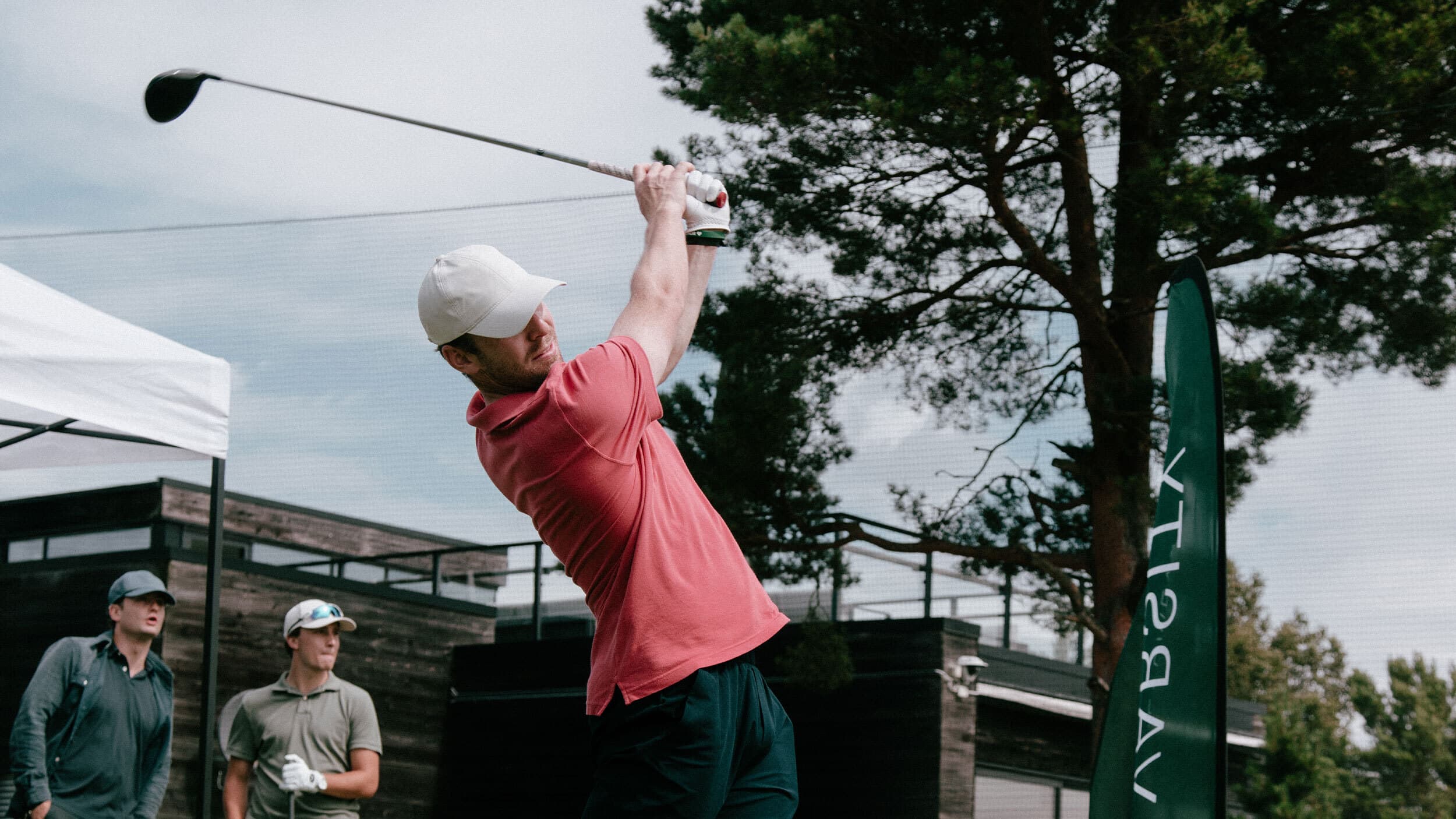
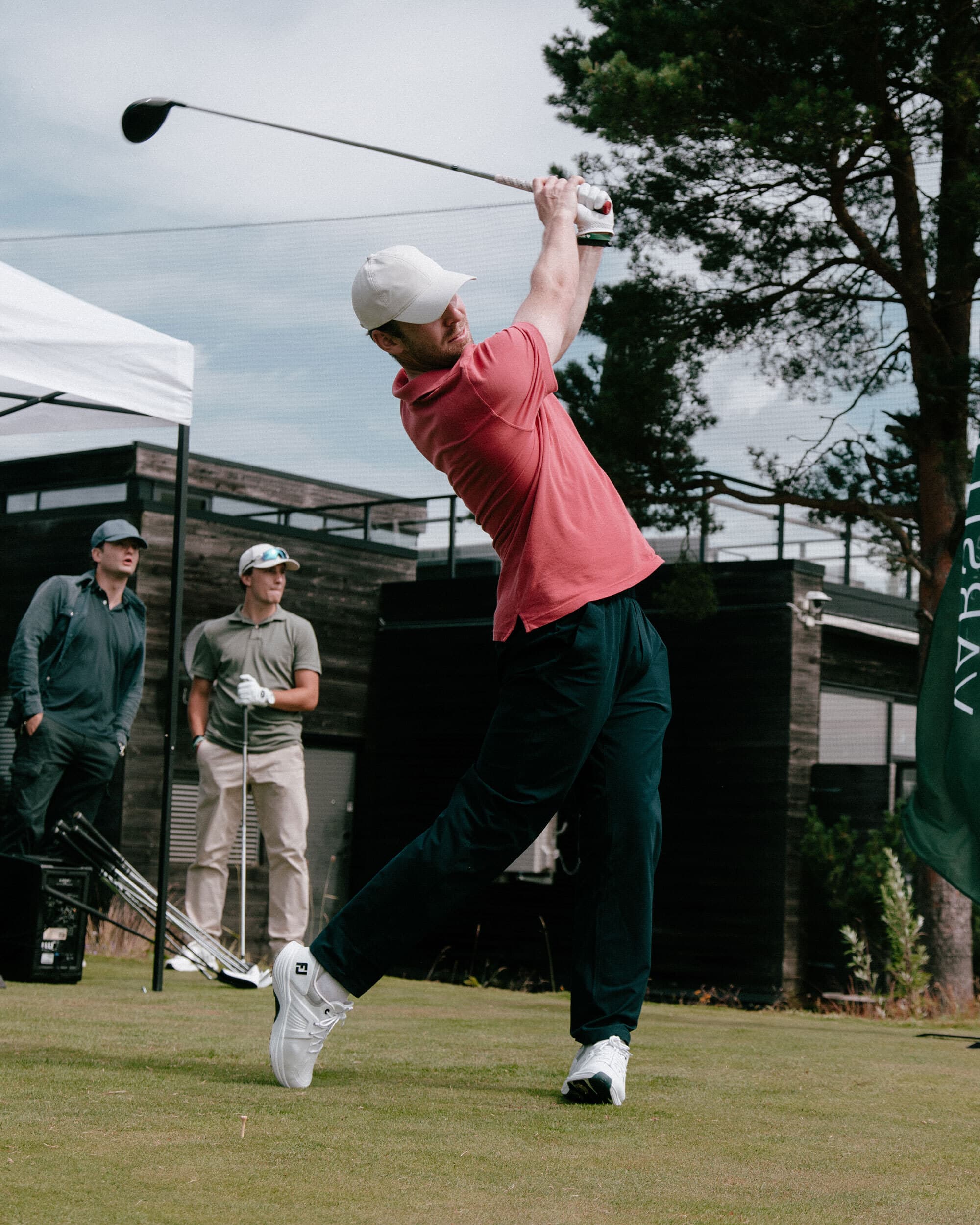
Owners Club Experience: Wright Invitational
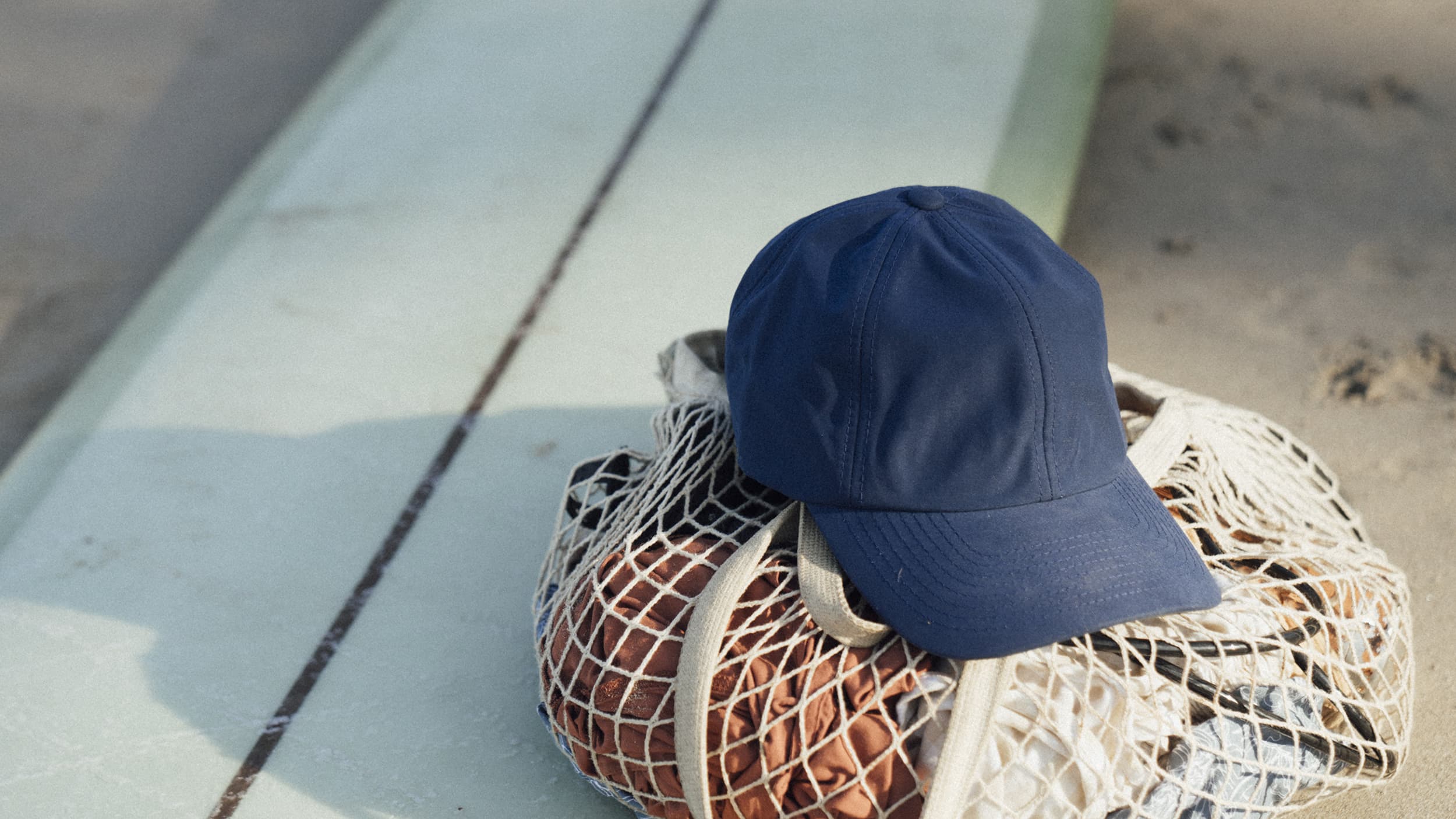
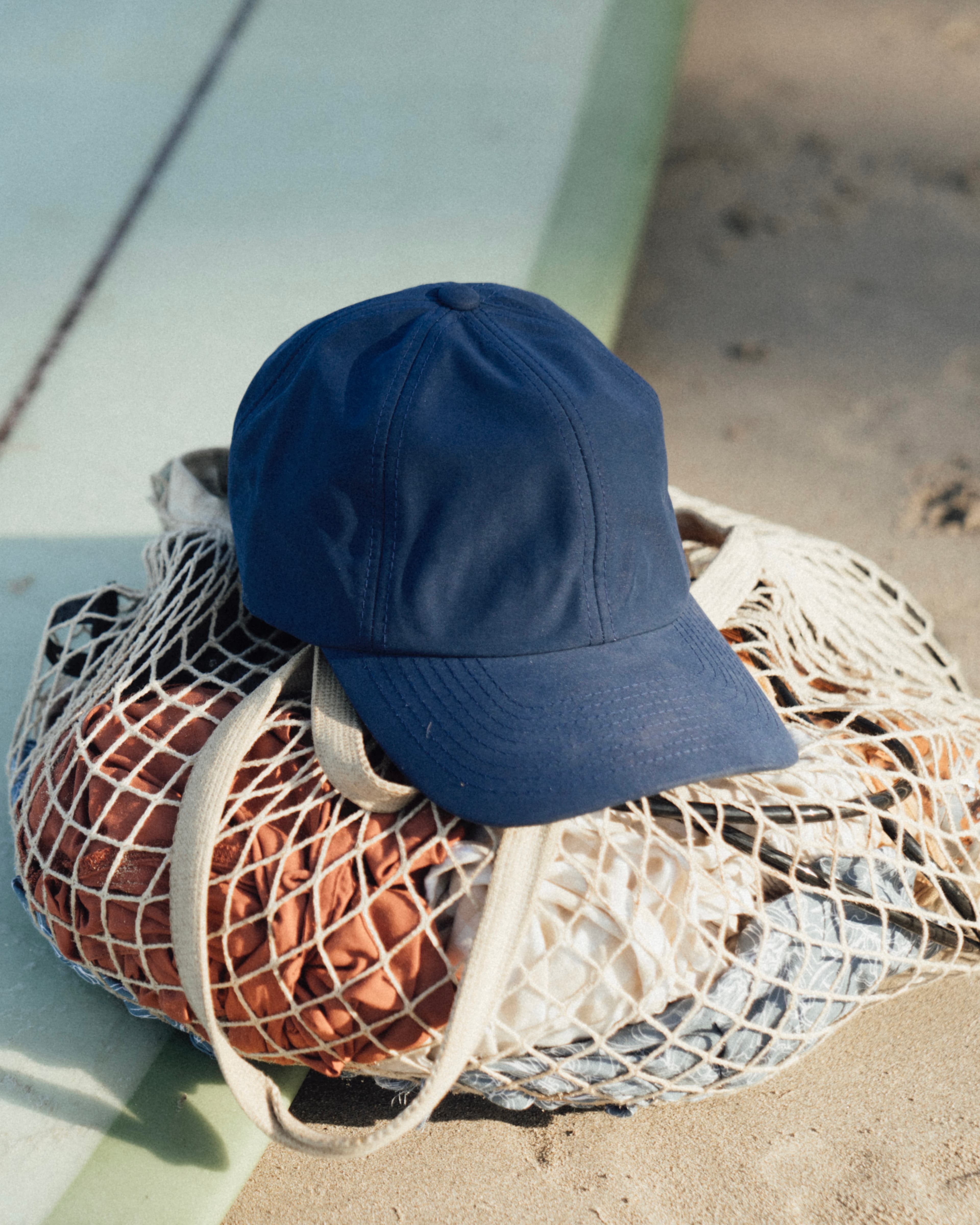
Seaqual: Best Caps for Summer
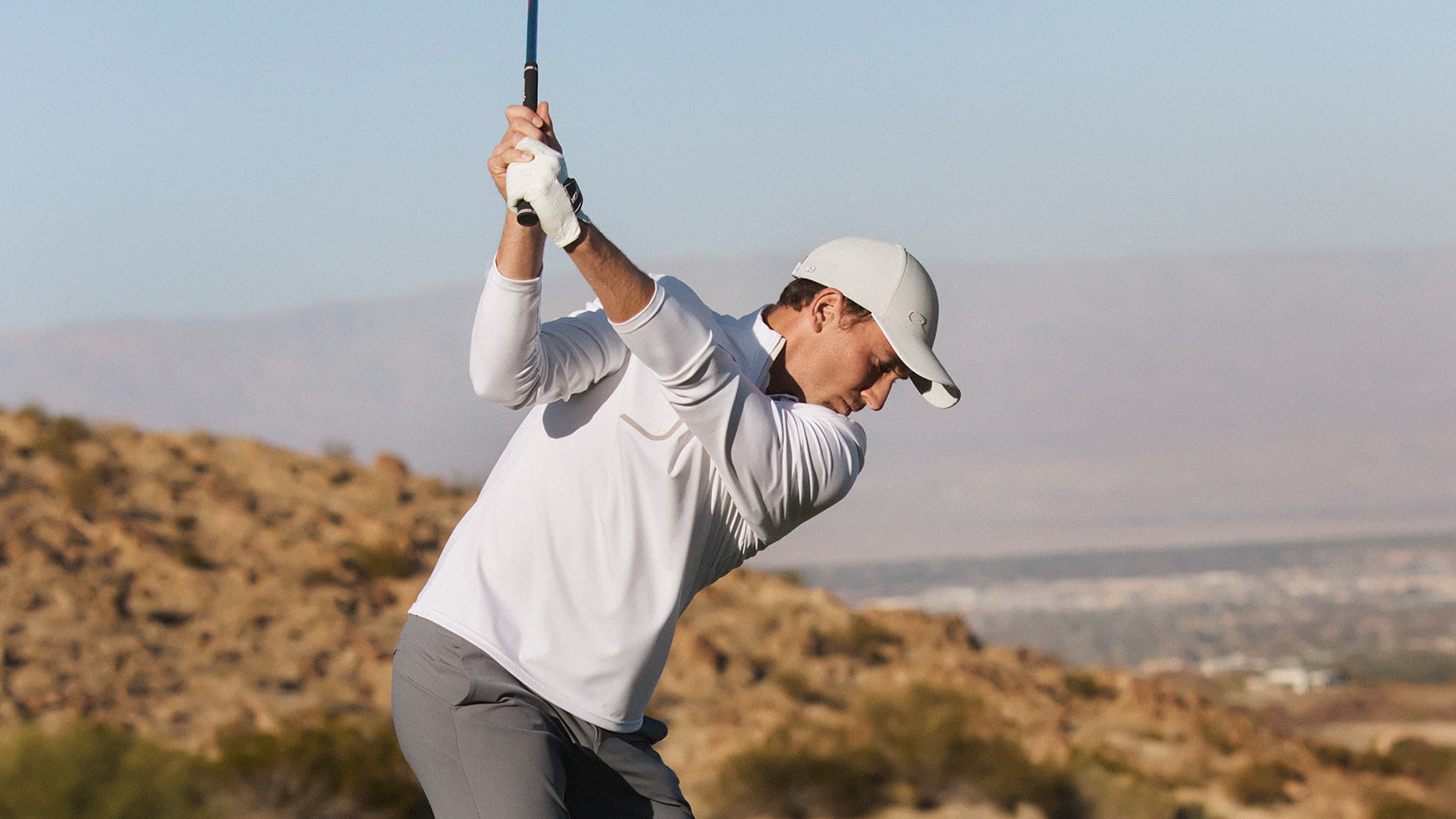
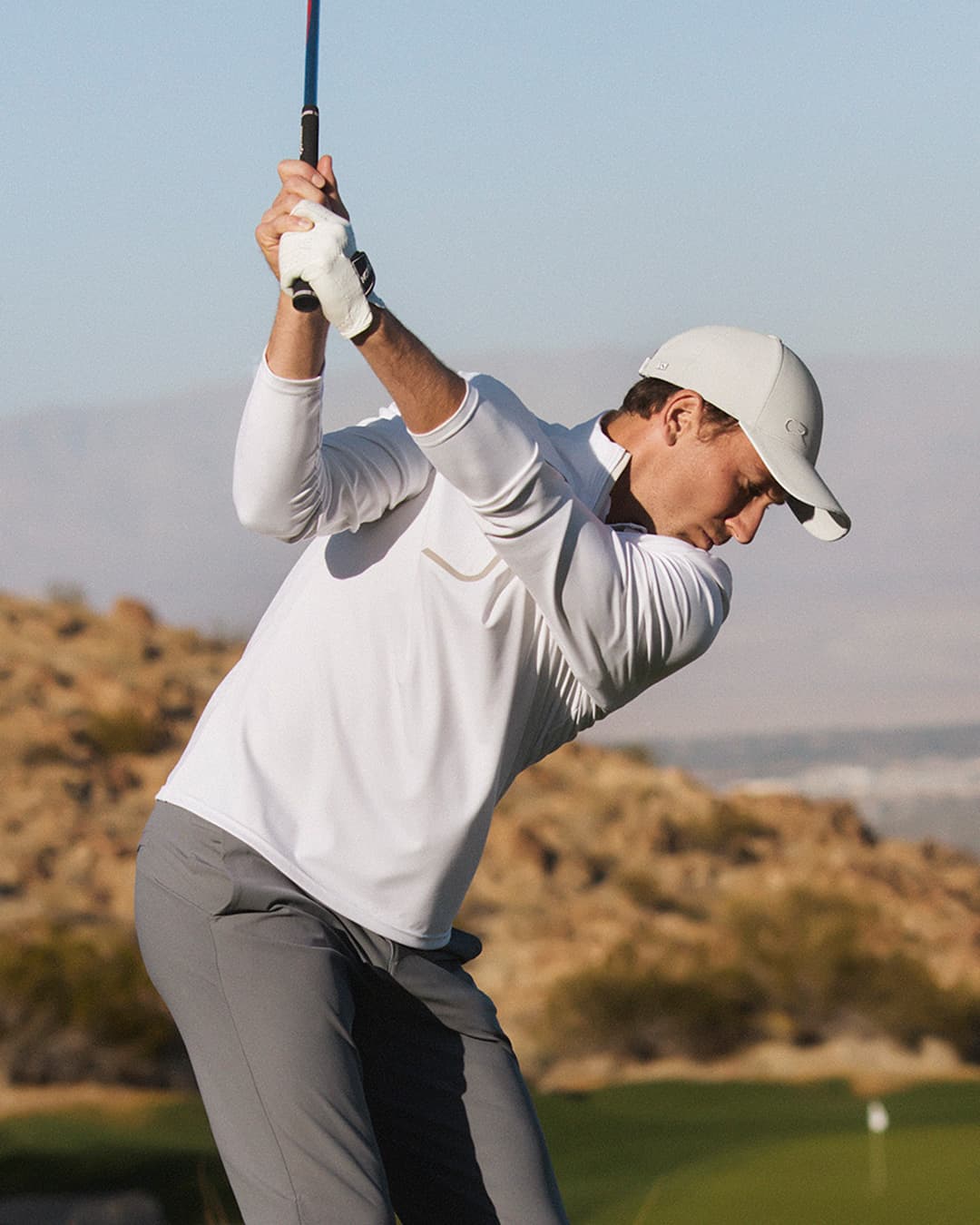